Prof. Dhiraj Kumar Mahajan
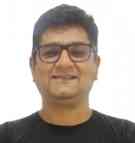
R. No. 329, Satish Dhawan Block
Professor
Mechanical
Mobile: +91-7814252244
dhiraj.mahajan @ iitrpr.ac.in
Prof. Mahajan’s Short Biodata:
Prof. Mahajan is a Professor in the Department of Mechanical Engineering at IIT Ropar and an interdisciplinary researcher with a strong interest in translational research, focusing on transforming laboratory innovations into real-world products and solutions. He is also an Associate Faculty Member at the Centre of Research for Energy Efficiency and Decarbonization (CREED) and Centre for Applied Research in Data Sciences (CARDS). Recently, he has also been associated with the PU-IIT Ropar Regional Accelerator for Holistic Innovations Foundation (PI-RAHI) as the Lead Faculty Member for Sustainable Mobility and Green Energy. His research spans diverse areas, including Hydrogen Technologies, Medical Devices, Sustainability, Energy Transition, and Applied AI/ML. For regular updates about his professional journey, you can connect with him on LinkedIn. His Google Scholar profile can be accessed [link] to explore his latest research contributions.
Prof. Mahajan’s Pedagogy:
He follows a student-centric and research-driven teaching approach that blends theoretical concepts with practical applications. His classes emphasize experiential learning, problem-solving, and connecting classroom knowledge with real-world challenges. He encourages students to participate in projects, research discussions, and hands-on activities to develop critical thinking and innovation.
Prof. Mahajan’s Academic Lineage:
Before joining IIT Ropar as an Assistant Professor in 2013, he worked as a postdoctoral researcher at the Interdisciplinary Centre for Advanced Materials Simulation (ICAMS), Ruhr University Bochum, Germany, under the guidance of Prof. Alexander Hartmaier, focusing on advanced topics in materials science. He earned his Bachelor of Technology in Production Technology from Punjab Technical University and a Master of Technology in Advanced Manufacturing Processes from NIT Warangal. He completed his PhD in Solid Mechanics at IIT Kanpur in 2010 under the supervision of Prof. Sumit Basu.
Prof. Mahajan’s Research Output:
Prof. Mahajan is working on several sponsored and consultancy projects (worth 60 million Indian Rupees) related to the design and development of fuel cell electric vehicles, Type IV hydrogen tanks, and AI/ML-based polymer membrane material discovery for fuel cells, along with their optimised metallic bipolar plates, hydrogen embrittlement-resistant steels, bioresorbable coronary stents using microinjection moulding, sustainability studies and design of engineering systems for various state/national/private bodies. He has recently started working on Solid State Battery research work based on his strengths in developing novel polymer membranes and electrodes required for such energy storage devices. Lastly, he is looking into applications of AI/ML in energy transition. Following is his publication/patent tally so far:
+ Research Papers: 43
+ Books: 4 (Chapters)
+ Patents: 3 granted, 4 filed
+ Conference Publications: 12
Prof. Mahajan’s Entrepreneurship Journey:
Prof. Mahajan is the co-founder of two startups incubated at IIT Ropar: Ares Systems Pvt. Ltd. and Bodyloop Labs Pvt. Ltd. Ares Systems focuses on the development of novel hydrogen electrolysers, while Bodyloop Labs is dedicated to creating advanced medical devices that continuously relay critical biomarker information to support lifestyle improvement and preventive healthcare.
Administrative Assignments of Prof. Mahajan:
Institute Level Administrative Assignments:
+ Professor-Incharge (PIC) for Dr. Ranbir Singh Tinkerers’ Lab (established through Makers Bhawan Foundation as philanthropic contribution by Dr. Ranbir Singh, alumni of IIT Delhi) from Dec’24 onwards.
+ Head, Training & Placement Cell, Career Development & Corporate Relations Centre, IIT Ropar from Apr’17-Jul’21. Brought several reforms in the functioning of T&P Cell. Played a key role in establishing Career Development & Corporate Relation Centre (CDCRC) at IIT Ropar and starting a B. Tech program with an Additional Internship as well as Joint Master's Thesis program for M. Tech students.
+ Chairperson, Career Development & Corporate Relations Centre, IIT Ropar from May’23-March’24.
+ Organizing Team Member for G20 event organized by IIT Ropar in Amritsar, March 2023.
+ Organizing Team Member for SAE-BAJA 2018 at IIT Ropar, Jan’ 17-Mar’18.
+ Faculty In-charge, Board of Cultural Activities (BOCA), IIT Ropar, Aug'14 - Jun’15.
+ Established an online teaching feedback mechanism for IIT Ropar, June'14 - Nov’14.
Department Level Administrative Assignments:
+ Department Representative for Academic Council for Research & Post Graduate Studies (ACRPGS) from April 2020-January 2023.
+ Department Representative for Academic Council for Research & Post Graduate Studies (ACRPGS) for Center of Research in Energy Efficiency and Decarbonization (CREED) from May’24 onwards.
Prof. Mahajan’s Outreach Activities:
+ Member of the TED 27 and TED 26 Sectional Committees of the Bureau of Indian Standards (BIS).
+ Member of the Safety, Cross-Cutting Analysis and Integration Subcommittee under the Advisory Group (AG) of the National Green Hydrogen Mission, formed by MNRE.
+ Member of the CII National Council on Energy Transition & Hydrogen (2025–26) – a CEO Forum guiding policy advocacy for this key sector.
+ Member of the CII Taskforce on Green Hydrogen for the years 2022–23, 2023–24, and 2024–25.
+ Member of the CII National Committee on Future Mobility & Battery Storage for the years 2021–22 and 2022–23.
+ Panel member for the revision of IS 16735:2018 – “Cylinders for On-board Storage of Compressed Gaseous Hydrogen and Hydrogen Blends as a Fuel for Automotive Vehicles – Specification.”
+ Convenor of Panel 4 in TED 27 SC of BIS for reviewing standards related to EV electronic components and systems (PHS, BMS, controllers, and sensors).
Prof. Mahajan’s Community Service Roles:
+ Conducted GIAN course naming “Applied Fatigue and Fracture Mechanics” with Course Area: Mechanical Sciences & Infrastructure by Foreign Faculty: Richard Pettit from United States of America from the 16-05-2016 to 21-05-2016.
+ Organizing team member for “Advances in Robotics” conference organized at IIT Ropar from July 5-8, 2023.
+ Coordinator of AWaDH (Agriculture and Water Technology Hub, IIT Ropar) Internship Carnival in which we trained 100 students from all over India (online mode) from May21-August’21 (80+ patent applications submitted by interns based on their 8-week work in this internship carnival).
+ Coordinator, National Resource Centre for Manufacturing at IIT Ropar from Aug'18-Jul'19 to develop a 20-hour MOOC on Manufacturing. This course is floated on the Swayam Platform by GoI and includes extensive inputs from thought leaders from Industry and Academia.
+ Coordinator. AIDOTHON-2022 and AIDOTHON-2023, a summer internship program for S.T.E.M and Medical Sciences students conducted in collaboration with GnSkD Foundation (A Not-for-Profit Company registered with the Ministry of Corporate Affairs).
+ Coordinator of Energy Mentors (USA)-IIT Ropar online summer internship program for 2023 (Links to read interns testimonials: Link 1, Link 2)and 2024 editions. This is an international internship program in which 90 students participated in 2023 edition and 50 students participated in 2024 edition.
Prof. Mahajan’s Publications in Different Forums:
+ Article published by EVReporter.com on FAQs on Hydrogen Fuel Cell Technology (Link).
+ Article published by Blue Circle Community on Hydrogen Powered EVs: Possibilities Ahead (Link).
+ An assessment report on the achievement of DLI#4 (Share of participating institutes in the Focus States that train final-year engineering students to take exit examination (e.g. GATE, employability skill test, campus placement test, etc.)) submitted to the National Project Implementation Unit (NPIU) for evaluation of The Technical Education Quality Improvement Programme Phase III (TEQIP III) project undertaken by the Ministry of Human Resource Development, Government of India with assistance from the World Bank.
Prof. Mahajan’s Work Recognition:
+ Best Poster Award at DAE-BRNS Symposium on Multiscale Modeling of Materials and Devices (MMMD-2014) held at Bhabha Atomic Research Centre (BARC), Mumbai from October 30-November 2, 2014.
+ The work done on the Low-Cost Negative Pressure Room during the Covid-I outbreak was appreciated by MHRD minister, Dr Ramesh Pokhriyal Nishank, in his tweet (@DrRPNishank) on April 4th, 2020 (Related News article link)
+ IIT Ropar student team led by me as advisor won the second prize in HY Contest-2019 organized by the Hydrogen Association of India for the report titled "Modeling the Hydrogen Refuelling Station for Heavy Duty Bus Applications".
+ IIT Ropar student team led by me as advisor won the Veziroglu Award in HY Contest-2017 organized by the Hydrogen Association of India for the report titled "An Innovative Fuel Cell Application for Rural India: From Concept to Design".
+ IIT Ropar student team led by me as advisor won the second prize in HY Contest-2015 organized by Hydrogen Association of India for the report titled "Hydrogen Refueling Dispensing Station Model".
List of Government Sponsored Projects of Prof. Mahajan:
S.No. |
Title |
Sponsoring Agency |
Duration |
Role: Principal Investigator (PI) / Consultancy Incharge (CI) |
Outcome of the project |
1 |
Biodegradable Polymeric Stents: From Synthesis of Functionalized Raw Material to its Fabrication using Micro Injection Moulding Process |
DST Advanced Manufacturing Technology Program |
2018-2022 |
PI |
In this project, India's first cardiovascular plastic based bioresorbable stent was developed using microinjection molding process |
2 |
IIT Ropar as National Resource Centre for Manufacturing |
MHRD |
2018-19 |
PI |
Developed 20 hours MOOC Course floated on Swayam platform on Manufacturing with 5 hours video content by Industry leaders in various domains of Manufacturing |
3 |
Additive Manufacturing & Machine Learning based Development of Indigenous Hydrogen Fuel Cell Stack |
DST |
Ongoing |
PI |
In this ongoing project, novel polymer electrolyte membranes are development using material discovery through Machine Learning framework along with the ongoing work of developing a 100W fuel cell using additive manufacturing |
4 |
Development of an Effluent Treatment Plant for Hand tool Industry |
Uchchatar Avishkar Yojana (MHRD-DST-MSME) |
2016-2021 |
PI |
In this work, effluent treatment process is proposed based on newly developed Ion Exchange Resins suitable for treating concentrated nickel and concentrated chromium effluents (as per the approved objectives of the project) within the premises of the industry partner. |
5 |
Study of the Effect of Microstructure on Fatigue Crack Initiation in Nickel under Hydrogen Environment using Coupled Framework of Crystal Plasticity & Hydrogen Transport Mode |
DST-SERB |
2015-2019 |
PI |
In this work, a novel multiphysics model was proposed to understand hydrogen embrittlement phenomena in metals based on Crystal Plasticity Finite Element Framework |
6 |
Design, development, and demonstration of indigenous hydrogen storage and fuel cell system for mobile and stationary applications of 5 kW capacity |
IMPRINT-MHRD |
2017-2022 |
Co-PI |
In this project, a prototype of 18 liters Type IV tanks was developed using pre-manufactured plastic liners from abroad while designing of composite winding was done in-house along with end-to-end manufacturing and burst testing done in India. |
7 |
Grant under the fund for the improvement of S&T infrastructure (FIST). |
DST |
2015-2020 |
Co-PI |
I was responsible for establishing |
List of Industry Consultancy or CSR Projects of Prof. Mahajan:
S.No. |
Title |
Sponsoring Agency |
Duration |
Role: Principal Investigator (PI) / Consultancy Incharge (CI) |
Outcome of the project |
1 |
Synthesis and validation of germicidal coating for BOPP films |
Max Speciality Films Limited (MSFL), Nawanshahr, Punjab |
2022 |
Co-CI |
In this work, novel anti-viral coatings were developed for controlling corona virus spread through plastic packaging |
2 |
Design Support for Negative Pressure Ambulance and Isolation Room for Covid19 Patients |
Bafna Healthcare Pvt. Ltd. |
April 2021-August 2021 |
CI |
In this work, India's first negative pressure ambulance was developed for transporting patients suffering from contagious diseases (Related Links: Link-1, Link-2) |
3 |
Design and development of a customized elastomeric balloon for a constant air pressure output bio-medical device |
COEO Labs |
2016 |
CI |
In this work, novel elastomeric balloons were developed that were used to develop a medical device naming SAANS which is a low cost multi powered neonatal transport CPAP |
4 |
Development of Gas Driven Mini-Turbine for Automotive Applications |
Enerstrong Technologies Pvt. Ltd |
2021-ongoing |
CI |
In this ongoing project, a mini turbine that uses high pressure gas to generate electricity is being developed for automotive applications |
5 |
Designing of gas turbines for energy storage |
EarthEn Inc (USA based startup) |
2022-23 |
CI |
In this project, design work of super critical CO2 based turbine was performed |
6 |
Projects through CSR funding from ANSYS to work on the development of two biomedical products |
CSR Project: Ansys Softwares Pvt. Ltd (India) |
2020-2022 |
PI |
In this CSR project, Ansys supported development of two novel medical devices for which patents are filled |
7 |
Independent Verification Agency for Technical Education Quality Improvement Programme-III executed by NPIU |
MHRD & World Bank |
2018-19 |
CI |
In this project, the output of TEQIP-III program of MHRD & World Bank related to GATE examination training was verified in more than 100 colleges as Independent Verification Agency. |
8 |
Establishment of NABL Accredited Sustainability Laboratory at IIT Ropar |
CSR Project: Toppan Speciality Films Limited (TSFL, previously MSFL), Nawanshahr, Punjab |
2023-ongoing |
PI |
In this ongoing CSR project, I am responsible for establishing a NABL accredited Sustainability Laboratory dealing with biodegradability testing of plastics and promoting the use of hydrogen a zero-emission solution for industry |
9 |
Feasibility Study – Converting non-recyclable plastic into green hydrogen |
FCDO representing the government of U.K. of Great Britain and Northern Ireland |
2023-24 |
CI |
A feasibility study was performed to evaluate various technologies for converting non-recyclable plastic into green hydrogen including their techno-commercial aspects |
10 |
“Design, development & testing of low-cost drug-eluting polymer based bioresorbable coronary stents using micro-injection molding process” through CSR support of Dassault Systemes Foundation, |
CSR Project: Dassault Systemes Foundation, Pune |
2025 |
CI |
Preclinical trials of developed stents will be performed in this CSR project |
11 |
AICTE-QIP-PG Certificate Programme session 2025-26 in Hydrogen Energy Technology |
AICTE |
2026 |
Program Coordinator |
18 credit courses for faculty members from AICTE affiliated colleges will be developed and run at IIT Ropar under this project |
12 |
Support for Design and Development of 1.5 kW and 15 kW Graphite bipolar plates-based Fuel Cells and their integration in Fuel Cell Electric Vehicles |
NTF (INDIA) Private Limited 400, Sector-8, IMT Manesar, Gurgaon-122050, Haryana |
2025 |
CI |
Indigenous Fuel cells and Fuel cell vehicles will be developed in this project for NTF |
13 |
Design of in-situ water channel fabricator with in-build batching plant |
Punjab Water Resources Management & Development Corporation Limited |
2024 |
CI |
Novel engineering design of in-situ water channel fabricator is proposed in this project |
List of Journal Publications of Prof. Mahajan
S. No. |
Journal Name |
Title |
Year of Publication |
Authors or Co-Authors |
Impact factor |
1 |
Polymer |
Micromechanics of the growth of a craze fibril in glassy polymers |
2005 |
Basu S.; Mahajan D.K.; Van Der Giessen E. |
4.1 |
2 |
Journal of the Mechanics and Physics of Solids |
Ageing and rejuvenation in glassy amorphous polymers |
2010 |
Mahajan D.K.; Estevez R.; Basu S. |
5 |
3 |
Modelling and Simulation in Materials Science and Engineering |
Investigations into the applicability of rubber elastic analogy to hardening in glassy polymers |
2010 |
Mahajan D.K.; Basu S. |
1.9 |
4 |
Physical Review E - Statistical, Nonlinear, and Soft Matter Physics |
Coarse-graining scheme for simulating uniaxial stress-strain response of glassy polymers through molecular dynamics |
2010 |
Majumder M.K.; Ramkumar S.; Mahajan D.K.; Basu S. |
2.2 |
5 |
International Journal of Applied Mechanics |
On the simulation of uniaxial, compressive behavior of amorphous, glassy polymers with molecular dynamics |
2010 |
Mahajan D.K.; Basu S. |
2.9 |
6 |
Physical Review E - Statistical, Nonlinear, and Soft Matter Physics |
Void nucleation and disentanglement in glassy amorphous polymers |
2010 |
Mahajan D.K.; Singh B.; Basu S. |
2.2 |
7 |
Physical Review E - Statistical, Nonlinear, and Soft Matter Physics |
Mechanisms of crazing in glassy polymers revealed by molecular dynamics simulations |
2012 |
Mahajan D.K.; Hartmaier A. |
2.2 |
8 |
Modelling and Simulation in Materials Science and Engineering |
A scheme to combine molecular dynamics and dislocation dynamics |
2012 |
Brinckmann S.; Mahajan D.K.; Hartmaier A. |
1.9 |
9 |
International Journal of Pressure Vessels and Piping |
Role of prior austenite grain boundaries in short fatigue crack growth in hydrogen charged RPV steel |
2019 |
Singh R.; Singh A.; Singh P.K.; Mahajan D.K. |
3 |
10 |
International Journal of Hydrogen Energy |
Hydrogen induced blister cracking and mechanical failure in X65 pipeline steels |
2019 |
Singh V.; Singh R.; Arora K.S.; Mahajan D.K. |
8.1 |
11 |
Modelling and Simulation in Materials Science and Engineering |
Role of stress triaxiality on ductile versus brittle fracture in pre-cracked FCC single crystals: An atomistic study |
2019 |
Singh R.; Mahajan D.K. |
1.9 |
12 |
Materials Chemistry Frontiers |
A carbon quantum dot and rhodamine-based ratiometric fluorescent complex for the recognition of histidine in aqueous systems |
2019 |
Singh H.; Sidhu J.S.; Mahajan D.K.; Singh N. |
6 |
13 |
International Journal of Pressure Vessels and Piping |
Effect of microstructural features on short fatigue crack growth behaviour in SA508 Grade 3 Class I low alloy steel |
2020 |
Singh R.; Singh A.; Singh P.K.; Mahajan D.K. |
3 |
14 |
Journal of the Mechanics and Physics of Solids |
Hydrogen distribution in metallic polycrystals with deformation |
2020 |
Kumar R.; Mahajan D.K. |
5 |
15 |
Journal of Nuclear Materials |
In-situ investigations of hydrogen influenced crack initiation and propagation under tensile and low cycle fatigue loadings in RPV steel |
2020 |
Singh R.; Singh V.; Arora A.; Mahajan D.K. |
2.8 |
16 |
Sensors and Actuators, B: Chemical |
A low-cost device for rapid ‘color to concentration’ quantification of cyanide in real samples using paper-based sensing chip |
2020 |
Singh H.; Singh G.; Mahajan D.K.; Kaur N.; Singh N. |
8 |
17 |
Materials Science and Engineering: A |
Towards the prediction of intergranular fatigue crack initiation in metals due to hydrogen |
2020 |
Arora A.; Singh H.; Mahajan D.K. |
6.1 |
18 |
Computational Materials Science |
On the transition of fracture toughness in metallic materials with thickness: An atomistic viewpoint |
2020 |
Singh R.; Mahajan D.K. |
3.1 |
19 |
Tribology International |
Cavitation erosion resistant nickel-based cermet coatings for monel K-500 |
2021 |
Singh N.K.; Ang A.S.M.; Mahajan D.K.; Singh H. |
6.1 |
20 |
Journal of Thermal Spray Technology |
Characterization and Slurry Erosion Mechanisms of Nickel-Based Cermet Coatings on Monel K-500 |
2021 |
Singh N.K.; Kumar A.; Ang A.S.M.; Mahajan D.K.; Singh H. |
3.2 |
21 |
Philosophical Magazine |
Effect of stable stacking fault energy and crystal orientation on fracture behaviour of thin metallic single crystals |
2021 |
Singh R.; Mahajan D.K. |
1.5 |
22 |
Theoretical and Applied Fracture Mechanics |
Hydrogen assisted crack initiation in metals under monotonic loading: A new experimental approach |
2021 |
Arora A.; Kumar R.; Singh H.; Mahajan D.K. |
5 |
23 |
Carbon Trends |
Effect of multi-walled carbon nanotubes on DC electrical conductivity and acetone vapour sensing properties of polypyrrole |
2022 |
Husain A.; Mahajan D.K. |
3.1 |
24 |
Surface and Coatings Technology |
Cavitation erosion mechanisms of HVOF-sprayed Ni-based cermet coatings in 3.5% NaCl environment |
2022 |
Singh N.K.; Vinay G.; Ang A.S.M.; Mahajan D.K.; Singh H. |
5.3 |
25 |
International Journal of Plasticity |
Coupled diffusion-mechanics framework for simulating hydrogen assisted deformation and failure behavior of metals |
2022 |
Singh V.; Kumar R.; Charles Y.; Mahajan D.K. |
9.4 |
26 |
Mechanics of Materials |
Modelling of hydrogen-assisted damage at the deforming single crystal crack-tip |
2023 |
Kumar R.; Mahajan D.K. |
3.4 |
27 |
Protection of Metals and Physical Chemistry of Surfaces |
Corrosion and Thermal Analysis of 316L Stainless Steel Coated PLA Parts Fabricated by FDM Process for Biomedical Applications |
2023 |
Kumar R.; Kumar M.; Chohan J.S.; Singh N.K.; Mahajan D.K. |
1.1 |
28 |
Diamond and Related Materials |
Corrosion behaviour of laser textured and WCCoCr+GNPs coated IS-2062 steel |
2023 |
Kumar V.; Singh N.K.; Verma R.; Mahajan D.K.; Sharma V.S. |
4.3 |
29 |
Transactions of the Indian National Academy of Engineering |
An Experimentally Informed Computational Framework for Investigating the Role of Surface Roughness on High Cycle Fatigue Life of LPBF IN718 |
2023 |
Kumar S.; Mahajan D.K; Bouhattate J.; Srinivasan D. |
- |
30 |
Chemical Engineering Journal |
Atomistic simulation and synthesis of novel sulfonated Polyimide polymer electrolyte membranes with facile proton transport |
2023 |
Rohilla T.; Husain A.; Singh N.; Mahajan D.K. |
13.3 |
31 |
Modelling and Simulation in Materials Science and Engineering |
On the role of vacancy-hydrogen complexes on dislocation nucleation and propagation in metals |
2023 |
Arora A.; Singh H.; Adlakha I.; Mahajan D.K. |
1.9 |
32 |
International Journal of Hydrogen Energy |
Hydrogen-assisted intergranular fatigue crack initiation in metals: Role of grain boundaries and triple junctions |
2023 |
Kumar R.; Arora A.; Mahajan D.K. |
8.1 |
33 |
International Journal of Fatigue |
Fatigue response of glass-filled epoxy composites: A crack initiation and propagation study |
2023 |
Arora A.; Sharma A.; Singh M.; Mahajan D.K.; Kushvaha V. |
5.7 |
34 |
Computational Materials Science |
Designing sulfonated polyimide-based fuel cell polymer electrolyte membranes using machine learning approaches |
2023 |
Rohilla T.; Singh N.; Krishnan N.C.; Mahajan D.K. |
3.1 |
35 |
Journal of Science: Advanced Materials and Devices |
Harnessing sustainable N-doped activated carbon from walnut shells for advanced all-solid-state supercapacitors and targeted Rhodamine B dye adsorption |
2024 |
Husain A.; Ansari K.; Mahajan D.K.; Kandasamy M.; Ansari M.N.M.; Giri J.; Al-Lohedan H.A. |
6.7 |
36 |
Dalton Transactions |
Facile synthesis of a three-dimensional Ln-MOF@FCNT composite for the fabrication of a symmetric supercapacitor device with ultra-high energy density: overcoming the energy storage barrier |
2024 |
Khan M.Y.; Husain A.; Mahajan D.K.; Muaz M.; Shahid M.; Zeeshan M.; Sama F.; Ahmad S. |
3.5 |
37 |
Materials Science and Engineering: A |
Investigation into hydrogen assisted fracture in Nickel oligocrystals |
2024 |
Singh V.; Raj A.; Mahajan D.K. |
6.1 |
38 |
Journal of Science: Advanced Materials and Devices |
Harnessing sustainable N-doped activated carbon from walnut shells for advanced all-solid-state supercapacitors and targeted Rhodamine B dye adsorption |
2024 |
Husain A.; Ansari K.; Mahajan D.K.; Kandasamy M.; Ansari M.N.M.; Giri J.; Al-Lohedan H.A. |
6.7 |
39 |
Fatigue and Fracture of Engineering Materials and Structures |
Role of grain size and anisotropy of neighboring grains in hydrogen-assisted intergranular fatigue crack initiation in austenitic stainless steel |
2024 |
Arora A.; Singh M.; Nair V.; Singh H.; Mahajan D.K. |
3.373 |
40 |
International Journal of Hydrogen Energy |
Hydrogen embrittlement in Nickel oligocrystals: Experimentation and crystal plasticity-phase field fracture modeling |
2024 |
Singh V.; Raj A.; Charles Y.; Mahajan D.K. |
8.1 |
41 |
Surface and Coatings Technology |
Effect of prolonged immersion on corrosion and cavitation resistance of HVOF-sprayed WC-NiCr and WC-Hastelloy cermet coatings |
2024 |
Halder S., Vinay G., Anupam A., Ang ASM, Mahajan D. K., Singh H. |
5.4 |
42 |
Inorganic Chemistry Communications |
Attaining promising efficiency through a Quasi-Solid-State symmetrical supercapacitor and dye-sensitized solarcell counter electrode utilizing bifunctional Nitrogen-Doped microporous activated carbon |
2024 |
Husain A., Kandasamy K., Mahajan D. K., Selvaraj M, Ahmad R., Assiri M. A., Kumar N., Ramachandaramurthy V.K |
4.4 |
43 |
CIRP Journal of Manufacturing Science and Technology
|
Novel net-shape manufacturing of bioresorbable coronary stents using micro-injection molding process |
2025 |
Tyagi D.K.; Mahajan D.K.
|
4.6 |
Granted/Filed Patents of Prof. Mahajan
+ Patent Title: A Bioresorbable Cardiovascular Stent, Applicant: Indian Institute of Technology Ropar, Inventors: Dharmendra Kumar TYAGI & Dhiraj K. MAHAJAN, Date of Filing: 06/03/2024, Application No: 202411015887, Country of filing: India
+ Patent Title: Methodology to Extract Stress Maps from Electron Backscatter Diffraction Data, Applicant: Indian Institute of Technology Ropar, Inventors: Aman ARORA & Dhiraj K. MAHAJAN, Status: Granted, Patent No. 426533, Date of Filing: 07/03/2020, Date of Grant: 23/03/2023, Application No. 202011009920, Country of filing: India
+ Patent Title: Leak Proof Liner-Boss Assembly for Type IV Hydrogen Storage Tanks, Applicant: Indian Institute of Technology Ropar, Inventors: Dhiraj K. MAHAJAN, Srikant Shekhar PADHEE, Ravi Mohan PRASAD and Mukesh KUMAR, Status: Granted, Patent No. 478710, Date of Filing: 28/05/2020, Date of Grant: 07/12/2023, Application No. 202011022281, Country of filing: India
+ Patent Title: System for optimizing air pressure in a compartment and a method thereof, Applicant: Indian Institute of Technology Ropar, Inventors: Dhiraj K. MAHAJAN, Shubham SINGH, Mayank SRIVASTAV, Sofen Kumar JENA, Status: Filed, Date of Filing: 01-03-2022, Application No. 202211011084, Country of filing: India
+ Patent Title: A Lifecycle indicator for personal protective equipment and perishable objects and a method of configuring thereof, Applicant: Indian Institute of Technology Ropar, Inventors: Dhiraj Kumar MAHAJAN, Dhairya KATARIA, Pooja KULASHRI, Shubham SINGH & Ahmad HUSAIN, Status: Filed, Date of Filing: 15/02/2022, Application No. 202211007861, Country of filing: India
+ Patent Title: An autonomous system for low payload gripper changing mechanism and its method thereof, Applicant: Indian Institute of Technology Ropar, Inventors: Vineet YADAV, Harshal BHAT, Pradeep SAINI, Akshay VERMA, Jaideep AHER, Dhiraj Kumar MAHAJAN, Status: Granted, Patent No. 528223, Date of Filing: 05/01/2022, Date of Grant: 15/03/2024, Application No. 202211000649, Country of filing: India.
+ Patent Title: System and method for reducing degradation of proton-exchange membrane fuel cell components, Applicant: Indian Institute of Technology Ropar, Inventors:Kharak SINGH & Dhiraj K MAHAJAN, Status: Filed, Date of Filing: 26/12/2024, Application No. 202411103164, Country of filing: India
PhD Supervision by Prof. Mahajan:
S.No. |
Student Name |
Category (Fulltime/ Part-time/ ERP.. etc.) |
Thesis Title |
Status: Completed or In-Progress |
Co-Supervisors |
Date of Thesis Defended |
LinkedIn Profile |
1 |
Dr. Rajwinder Singh |
Fulltime |
Investigation into the Short Crack Nucleation and Propagation in Metals under Monotonic and Cyclic Loadin |
Completed |
- |
October 30, 2019 |
|
2 |
Dr. Rakesh Kumar |
Fulltime |
Micromechanical Modeling of Hydrogen assisted Crack Initiation in Metals under Monotonic and Cyclic Loading |
Completed |
- |
September 26, 2020 |
|
3 |
Dr. Harupjit Singh |
Fulltime |
Chemosensor Devices for Detection and Quantication of Analytes Using Multivariate Analysis and Machine Learning-Based Approaches |
Completed |
Prof. Narinder Singh |
7th March, 2022 |
|
4 |
Dr. Navneet Singh |
Fulltime |
Investigations on Cavitation Erosion of High-velocity Oxy-fuel (HVOF)-Sprayed Nickel-based Cermet Coatings on Monel K-500 Alloy |
Completed |
Prof. Harpreet Singh |
20th June 2022 |
|
5 |
Dr. Aman Arora |
Fulltime |
Role of metallic microstructure on hydrogen-assisted crack initiation under monotonic and cyclic loading |
Completed |
Prof. Harpreet Singh |
6th July, 2022 |
|
6 |
Dr. Tushita Rohilla |
Fulltime |
Data-driven and Simulation-assisted Synthesis of Hydrocarbon Polymer Electrolyte Membranes |
Completed |
- |
28th November, 2023 |
Link |
7 |
Dr. Vishal Singh |
Fulltime |
Micro-mechanical Analysis of Hydrogen Assisted Damage in Metallic Microstructures |
Completed |
- |
16th January 2024 |
|
8 |
Mr. Dharmendra Kumar Tyagi |
Fulltime |
On the Development of Bioresorbable Cardiovascular Using Micro-injection Molding Process |
Submitted |
- |
|
|
9 |
Mr. Akhilesh Kumar |
Part-time |
Design optimization of High-Power Density PEM Fuel Cells* |
In Progress |
|
|
Link |
10 |
Mr. Ajaya Jena |
Fulltime |
Design optimization of High-Pressure PEM Electrolyser |
In Progress |
|
|
Link |
11 |
Mr. Shubham Shandilya |
Fulltime in Centre for Applied Research in Data Sciences (CARDS)
|
AI/ML framework for predicting renewable energy generation based on weather* |
In Progress |
|
`Link |
|
12 |
Ms. Anita |
Fulltime in Centre of Research for Energy Efficiency and Decarbonization (CREED) |
Development of Polymer Electrolyte Membrane based Solid State Battery* |
In Progress |
|
*Thesis Proposal Seminar Pending
Post Doctoral Researcher Supervision by Prof. Mahajan:
S.No. |
Name |
Source of Funding |
Timeline |
Topic |
|
1 |
Dr. Ahmad Hussain |
Institute Post Doctorate Fellow |
2022-2024 |
Electrochemistry, Fuel Cells, Biomaterials. |
B. Tech and M. Tech students who have worked with Prof. Mahajan:
B.Tech. (Major Project) |
M.Tech. or Dual Degree (B.Tech+M.Tech) |
2014-15: Gaurav Jagannath Mahajan, Sachin Kumar, Tushar Chaudhary 2015-16: Kishan Govind, Vishal Goyal, Ishneet Singh, Sumit Dahiya, Kuricheti Ravi Teja, Aashish kholiya, Maneesh Verma, Sajeed Mahaboob, Krishanu Sarkar, Adarsh Kumar 2016-17: Peeyushi Raghav, Anshu Kaushal, Jitin Madhu, Paryant Pradhan, Shivam Jindal, Prasoon Ratnam, Randhir Swarnkar, Ranjan Kumar, Tijender Singh, Gaurav Behrani, Vishal Gupta; 2017-18: Amanjot Singh, Deepesh Meena, Pradeep Kalra, J Sai Nitin, Swapnil Rai 2018-19: Aakash Ravgotra, Anuj Kalsotra, Harsha B T, Rishabh Anchalia, Rishabh Goel, Ritik Rai, Rushit Virani 2020-21: Ujwal Goel, Abhinash Barnwal; 2021-22: Sahil Dighe, Roshan Kumar Parihar, Saaransh Agarwal, 2022-23: Aswin, Aryan Anand, Hrithik Gupta, Harshpreet Singh, Akshit Mehra, Goutam Sharma, Bharat Kumawat, Akshay Kumar, Nishant Kumar Singh, Himanshu Dhiman 2023-24:Sudarshan Ramesh, Debjit Bhowal, Ankur Bharali, Anish Barna, Pradeep Tripathi, Sehajpreet Singh, Ankit, Ashok Kumar Saini, Emmanuel Lalrinchhana, Nitin 2024-25: Charukant, Pritam Dar, Harshita Sandhu, Devanshi Sawhney, Pranav Khurana, Vaishnavi Baredar |
2017: Mr. Shovit Sagar 2017:Mr. Mukesh Kumar 2017:Mr. Yashpal Singh 2019: Mr. Sandeep Mehla 2020: Mr. Mohd. Faizal 2020: Akash Bhardwaj 2020: Sumit Dahiya 2021: Yashjeet Chaudhary 2021: Ujwal Sontakke (External Candidate) 2022:Sanjay Barfa 2022: Mohit Deshmukh 2022: Mohit Singh 2022: Angaddeep Singh 2022: Dheeraj Kumar (External Candidate) 2024: Vivek Chanpa 2024: Ashutosh Singh 2024: Ayush Sharma 2024: Chailsy Sharma (External Candidate) 2024: Sharwan Godara 2024: Aniket Singh 2024: Amritanshu Khare 2025: Akshit Singh Thakur 2025: Barbie Borthakur 2025: Manas Bhatnagar 2025: Gaorav Vashistha |
+ Materials for high-pressure hydrogen storage
+ Hydrogen embrittlement of metals.
+ Development of novel polymers and composites for energy and biomedical applications
+ Energy Transition and Sustainability
+ Atomistic and Crystal Plasticity-based modeling of metal plasticity
Teaching Interests:
Management of Sustainable Development, Hydrogen Technologies, Crystal Plasticity, Applied Numerical Methods, Machine Design, Mechanics of Materials, Atomistic Modeling of Materials, Continuum Mechanics, Elasticity and Plasticity of Large Deformations, Fracture and Fatigue, Advanced Manufacturing Techniques.